Materia prima del acero
proveedores de materias primas siderúrgicas
El hierro reducido directamente (DRI) representa el 5% de los metales utilizados en el proceso de fabricación de acero en todo el mundo (Cuadro 1). Actualmente se utiliza menos que el arrabio o la chatarra. Tradicionalmente, el DRI se produce a partir de la reducción directa del mineral de hierro utilizando gas natural, pero la tecnología emergente está permitiendo la producción de DRI utilizando también hidrógeno. Dependiendo de la fuente de hidrógeno, esto ofrece el potencial de un acero verdaderamente verde. Por lo tanto, se espera que el DRI a base de hidrógeno sea una importante palanca de descarbonización para los fabricantes de acero, especialmente en Europa. Varias empresas ya han anunciado planes para introducir el DRI, y se espera un fuerte crecimiento en el futuro. De hecho, los escenarios basados en una industria siderúrgica neutra en carbono -un objetivo al que se han comprometido muchos grandes fabricantes de acero- prevén que la producción de DRI se triplique en los próximos 30 años.
A diferencia de la producción de arrabio de alto horno, el mineral de hierro se mantiene sólido durante todo el proceso de producción de DRI, lo que dificulta la eliminación de impurezas (Recuadro 2). En consecuencia, la calidad del DRI está estrechamente relacionada con la calidad del mineral de hierro utilizado. Por tanto, el DRI se fabrica principalmente con materias primas de muy alta calidad, que sólo pueden producirse en un número limitado de minas (Recuadro 3). Una expansión significativa de la industria del DRI provocará probablemente una escasez de materias primas en la próxima década. La base de datos MineSpans, que ofrece una visión completa de la oferta de la industria del mineral de hierro, deja claro que la oferta será insuficiente incluso si los fabricantes de acero utilizan plenamente las minas existentes y abren nuevas minas capaces de producir los insumos necesarios.
materia prima del hierro
El carbón es una parte fundamental del proceso de fabricación del coque. El carbón se tritura y se muele hasta convertirlo en polvo y, a continuación, se carga en un horno donde se calienta a unos 1800 °F en ausencia de oxígeno. A medida que se calienta el horno, el carbón empieza a fundirse, por lo que se elimina la mayor parte de la materia volátil, como el aceite, el alquitrán, el hidrógeno, el nitrógeno y el azufre. El carbón cocido, llamado coque, se retira del horno después de 18 a 24 horas de reacción. El coque se enfría y se criba en trozos de entre una y cuatro pulgadas. El coque es una roca negra, porosa y dura, de carbón concentrado (contiene entre el 90 y el 93% de carbono), que tiene algo de ceniza y azufre, pero que, en comparación con el carbón crudo, es muy fuerte. Los fuertes trozos de coque, con un alto valor energético, proporcionan la permeabilidad, el calor y los gases necesarios para reducir y fundir el mineral de hierro, las pellas y el sinterizado.
materia prima para la fabricación de acero ppt
En la actualidad, se calcula que la industria siderúrgica mundial utiliza unos 2.000 millones de toneladas de mineral de hierro, 1.000 millones de toneladas de carbón metalúrgico y 575 millones de toneladas de chatarra de acero para producir unos 1.700 millones de toneladas de acero bruto.
El acero reciclado (también llamado chatarra) es una de las materias primas más importantes de la industria. Procede de estructuras demolidas y de vehículos y maquinaria al final de su vida útil, así como de las pérdidas de rendimiento en el proceso de fabricación del acero.
La chatarra desempeña un papel fundamental en la reducción de las emisiones de la industria y el consumo de recursos. Cada tonelada de chatarra utilizada para la producción de acero evita la emisión de 1,5 toneladas de dióxido de carbono y el consumo de 1,4 toneladas de mineral de hierro, 740 kg de carbón y 120 kg de piedra caliza.
El mineral de hierro y el carbón metalúrgico se utilizan principalmente en el proceso de fabricación de hierro en altos hornos. Para este proceso, el carbón de coque se convierte en coque, una forma casi pura de carbono, que se utiliza como principal combustible y reductor en un alto horno.
Normalmente, se necesitan 1,6 toneladas de mineral de hierro y unos 450 kg de coque para producir una tonelada de arrabio, el hierro bruto que sale de un alto horno. Parte del coque puede sustituirse inyectando carbón pulverizado en el alto horno.
materia prima para la industria siderúrgica
Los minerales utilizados en la fabricación de hierro y acero son óxidos de hierro, que son compuestos de hierro y oxígeno. Los principales minerales de óxido de hierro son la hematita, que es el más abundante, la limonita, también llamada mineral marrón, la taconita y la magnetita, un mineral negro. La magnetita recibe su nombre por su propiedad magnética y tiene el mayor contenido de hierro. La taconita, llamada así por las montañas Taconic en el noreste de Estados Unidos, es un mineral de baja calidad, pero importante, que contiene tanto magnetita como hematita.
Para que los hornos de fabricación de hierro funcionen con eficacia, es necesario que el mineral tenga un contenido de hierro del 50% como mínimo. Además, el coste del transporte de los minerales de hierro desde la mina hasta la fundición puede reducirse en gran medida si la roca no deseada y otras impurezas pueden eliminarse antes del envío. Para ello, los minerales deben someterse a varios procesos denominados «de beneficio». Estos procesos incluyen la trituración, el cribado, el volteo, la flotación y la separación magnética. El mineral refinado se enriquece con más del 60% de hierro mediante estos procesos y a menudo se convierte en pellets antes de su envío. El polvo de mineral de taconita, tras el beneficio, se mezcla con polvo de carbón y un aglutinante y se enrolla en pequeñas bolas en un granulador de tambor donde se cuece hasta alcanzar la dureza. Por cada tonelada de pellets de taconita que se envía se retiran unas dos toneladas de material no deseado.
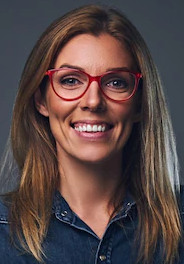
Bienvenid@, soy Patricia Gómez y te invito a leer mi blog de interés.